Automation Matters
3 Automation
Must-Haves
5 Reasons Why Automation Can Fail
AUTOMATION MATTERS
The downturn in international trade, re-imposing quarantine measures, and the overall health of the global economy are weighing on the onus of COVID-19 resurfacing in nations across the world. These irregularities continue to occur at a pace too quickly to countermeasure, which unfortunately forces impacted industry stakeholders to fall into voluntary administration. As a result, emphasis on technology to streamline processes and optimize operations have sparked interest amongst company executives as a sustainable alternative cultivating long-term competitiveness.
Businesses that already had established a strong technological presence experienced a less drastic transformation compared to impacted companies operating manually. Migrating workplace environments and operations entirely and purely into the cloud has driven business continuity and long-term benefits to maintain competitiveness. Likewise, automation has taken a more profound appreciation in this pandemic. Its ability to introduce a reformed procedure to digest big data, make informed and optimized decisions independently, will free up workloads to focus on other aspects of the business. A business embracing technology is fulfilling the cracks formed by the vulnerable system pre-pandemic and will create a well-integrated supply chain.
A digital business landscape developing into the new standard, and therefore, the absence of process automation will instigate challenges in all layers of an organization akin to communicating, reporting, managing, maintenance, etc. Automation technology embedded within a system infrastructure will harness operational efficiency from powering predictive analytics to improve business intelligence and make smarter decisions earlier.
Insufficient capital is an impediment terminal executives confront as the global economic crisis inflicts substantial financial pressures to remain afloat. After spending almost six months in worldwide calamity, encouraging future uptake in technologies like automation remains uncontested. Facing new business demands requires full technological embrace and trained staff to ensure the highest level of implementation success. However, projects require a relatively large budget. Consequently, immediate strategies are more straightforward, such as customizing existing packages or adopting new tools into legacy systems, instead of transforming from scratch. Therefore, this economic crisis has highlighted automation’s critical role in moving forward, but it is not a priority just yet.
The likelihood of the radical changes happening around the world settling anytime soon seem like a far-reaching reality. Throughout this period, it has exposed significant limitations inherent in manual business models and shed light in the necessary steps to progress and achieve a better-integrated supply chain. However, in the time of crisis, where companies need to cut expenses, automation may not be a priority – but it does matter.
3 AUTOMATION MUST-HAVES
Container terminals integrating some level of autonomy is inevitable with the increasing consumer demands forcing constant improvements upon the logistics chain. As a result, automation is introduced to container terminals to reform manual or inefficient operations. This surge in automation over the years have pushed new product rollouts across all sectors in the market, attempting to better process-, robotics-, devices-, and security-automation. With such a large selection, narrowing down the checklist for automation integration can be difficult. However, RBS has curated a list for the top 3 automation must-haves which achieve maximum operational- and cost-efficiency.
Removing the human interaction and assistance layer prevalent in CHEs and introducing automated equipment such as ARTGs and ARMGs will inherently improve productivity and container flow within the yard. This newly found independence in decision-making and work instruction execution contributes to lower accidents and higher turnover container rates. However, different terminals call for different degrees and types of automation. Which one are you?
RTG Terminal (Popular) → ARTG | RMG Terminal → ARMG |
Upgrading to an ARTG model ensures consistency in productivity and performance as information exchange is automatic and strategically calculated. ARTGs have the flexibility to manoeuvre and work in any area of the terminal, which is beneficial to any terminal size. | ARMGs have a high level of automation since it moves along a fixed track, making it easier to achieve automatic positioning and control as well as gaining full independence (in future). Running on electricity asserts it is a cost-effective and sustainable solution that prepares for the increase in fuel prices. |
Differential Global Positioning System (DGPS) is one of the best investment choices that unquestionably enhances automation capabilities as it detects motion and informs automated CHEs the correct movements to execute. It is used to avoid misplacement of containers, facilitate equipment routing, and optimize the dispatch of WI. Again, DGPS’ also removes the need for human interaction in functions alike loading and dispatching, leading to a decrease in error rate in storage handling while increasing the efficient turnover time of the container ships.
Without a Terminal Operating System (TOS) serving as the pillars to heed control and planning capabilities for container terminals, all operations and processes will be in complete chaos. Container terminals, therefore, must ensure their TOS supports their automation strategy. One of the biggest kept secrets that many unfortunately miss is that automation does not require a third-party interface to run automation capabilities. A reliable TOS should work standalone and directly communicate with the automated CHEs. Eliminating the unnecessary layer will provide real-time communication between the planning and execution phases. A true real-time architecture continues to be the most crucial aspect of any TOS, optimizing automation interactions and providing the foundation for achieving maximum efficiency.
The strategy to integrate automation starts with robotics and processes. Leverage these three must-haves to incite incredible results. Take due diligence and select reliable vendors to witness first-hand results.
5 REASONS WHY AUTOMATION CAN FAIL
Detect the factors which can contribute to terminal automation failure.
The introduction of automation capabilities has truly transformed conventional terminal practices. However, automation is still in its early stages regarding widespread adoption and incite a few challenges to any stakeholders who encounter the following:
- Non-real-time Communication in Equipment
There is several third-party software on the market, providing an interface with your TOS to the automation module. What terminal operators may misunderstand is that this third-party software adds a layer hindering direct real-time communication. As a result, CHEs in the terminal yard receive obsolete work instructions that incur additional re-handling instructions. Therefore, productivity drops 7-15% rather than increases in the presence of automation. The forged real-time connection in the equipment remains as one of the most significant root causes of automation failure.
- Poor Data Quality
Poor data quality arises as one of the most significant issues that ports and other organizations confront today when automation is not providing the expected results. It is the result of an absence in structure and visibility enforced in data, creating difficulty for immediate monitoring, and diagnosing of operations in the performance of equipment. Ports may also not be able to collect or exchange data optimally due to misalignment (or even absence) of standards, formats, and data structures, preventing a common data language. Poor data quality makes interfacing with a variety of equipment and systems complicated, costly, and risky. The risk of automation failure increases with most ports; according to the Mckinsey & Co survey declaring, they are liable to poor quality of data and the data analytics not being strong enough to operate automated ports effectively.
- Siloed Operations
The few automated container terminals operating today are closed systems that have been custom designed at high costs. These closed systems contribute siloed operations, which translate into operations unable to share information, tools, and processes with other procedures. The lack of interoperability causes information fragmentation and is difficult to contain within a specific process, which may spiral or evolve into more issues. The disconnect between different functions makes it more challenging to contain the arising problem within a process. Therefore, ports and terminals are unable to realize the full potential of automation.
- Shortage of capabilities
Startling statistics of the survey reveal the main issue preventing ports from experiencing the results they deserve is the lack of specialized positions left unfulfilled. Even the most experienced engineers can take as long as five years to train. Many ports have underestimated the process of procuring the required set of capabilities, particularly in planning and implementation. This alarming number not only details the reason for Automation failure but also calls for a new learning approach, such as online courses or hosting seminars, to bridge the gap of acquiring knowledge. However, a system or module requiring that long to train is an indicator the system is too complicated than necessary.
- Handling of Exceptions
A large amount of handling exceptions is indicative of a poor understanding of automating manual processes. If terminals are experiencing a decrease in efficiency, it is likely due to an increase in re-handling of exceptions. A fit TOS embedded with true automation capabilities will have dynamic work instructions, changing in real-time if needed as environmental conditions change.
We all can realize and curate a more robust understanding of automation through trials and test cases, and it offers an opportunity to improve on the knowledge foundation required in a TOS. The five reasons have helped RBS develop a fine-tuned, highly reliable, and powerful solution that rectifies the potential downturns while ensuring that terminal operators obtain the true benefits of automation.
GET UPDATES IN REAL-TIME
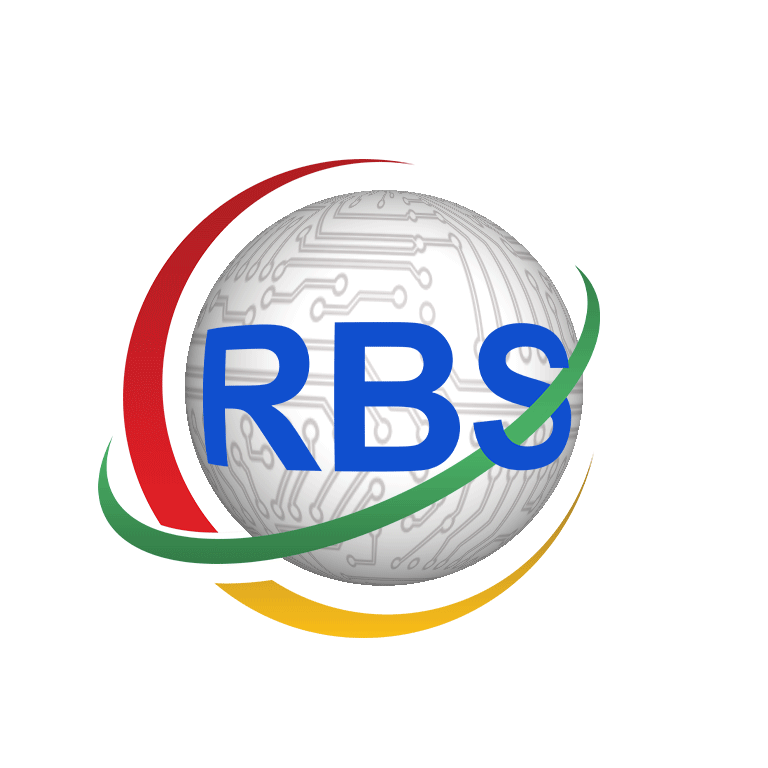